More Information
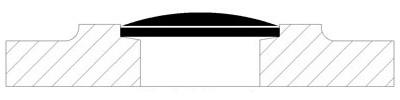
- The ground expansion plug offers the greatest level of holding power or leak resistance available in an expansion plug.
- The ground edge provides maximum contact surface area and finest surface finish.
- To maximize effect, the counter bore should receive special finishing.
- Ground Plugs, installed in a correctly prepared counter bore, should eliminate the need for sealer and should hold highly penetrating liquids.
- While their cost is higher than standard Hubbard Plugs, they are less expensive than pipe plugs or other closures when considering the total cost including tapping.
- We grind the edge circumferentially to a high finish, and segregate the parts when packing to prevent damage to the edge during shipment. For greatest protection ground edge Hubbard Plugs should be kept in their packing containers up to the point of assembly.
- We have found 1” diameter .083” thick steel ground plugs to hold 1,600 lbs of pressure before failure, which is between 10 and 20 times the holding power of a standard blanked edge plugs. The effective use range should be less than that.
Stock Materials
- Steel: SAE1008/1010 low carbon steel: ASTM#A109 or A569 depending on gage.
- Stainless Steel: 302 / 304 ASTM#A313
- Brass: ASTM#B36.
* These are materials we stock in various thicknesses. It does not mean we have finished inventory of all plugs in each of these materials.
** Customer specific materials different than those listed above are commonly run.
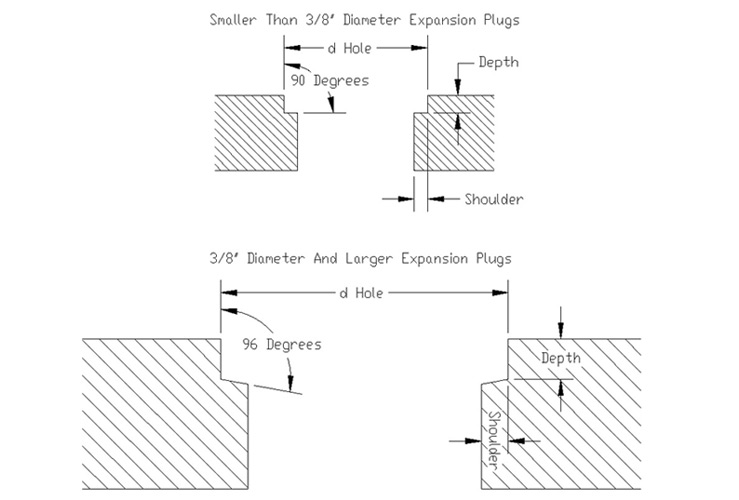
“d” Hole = Plug upper limit +.002”, more clearance may be needed for plugs over 2.5”.
Depth = 1-1/2 to 2 material thicknesses (1 material thickness minimum).
Shoulder = 1 material thickness
- The counter bore should be of a diameter that will take the plug without forcing, no larger. Typically this means .002” larger than the maximum plug diameter, although more clearance than .002” should be given to larger diameter plugs. If the plug is forced or press fit in the hole prior to expansion, the edge of the plug and the edge of the hole are apt to become marred, and leakage will occur.
- The counter bore should be round and free of tool chatter marks. 100 micro inches or smoother is a good finish guideline.
- The counter bore should be finished without any fillet. A fillet can prevent the proper seating of the plug. The counter boring tool should dwell long enough at the bottom of the counter bore to leave the bottom clean and smooth. The sharper the corner, the better the seal.
- The counter bore should be at least the depth of the material thickness of the plug to be installed.
- For the best condition, the width of the bottom of the counter bore should be approximately equal to the thickness of the plug to be used.
- For best results, the angle between the cylindrical sides and the bottom of the counter bore should be 95 to 97 degrees. This allows the plug to turn inside out slightly, and then spring back to an almost flat position – providing maximum sealing quality.
NOTE: The above hole configurations are for optimal sealing. Flat bottomed counter bores with varying shoulder widths are used for general sealing – applications with no liquid retention or pressure requirements.
DIN 470
The outside diameter (d) and spherical radius (r) of our metric plugs conforms to DIN 470 with no exceptions.
We offer many stock thicknesses and grades of material for each of these diameters – these stock grades and thicknesses do not always conform exactly to DIN 470.
The stock material grades we offer are listed under the “More Information” tab on this catalog page.
The stock material thicknesses that relate to each of these materials can be found by going through the RFQ process for a particular diameter of plug.
For quick reference, below is a table listing DIN 470 material thicknesses as well as the Hubbard Spring stock thicknesses for steel only:
Diameter (d) | Spherical Radius (r) | DIN470 Material Thickness (s) | Hubbard Stock Steel Thickness (s) |
3 | 3 | 0.8 | 0.64, 0.81 |
4 | 4 | 0.8 | 0.64, 0.81 |
5 | 6 | 0.8 | 0.64, 0.81 |
6 | 7 | 1.0 | 0.64, 0.81 |
8 | 9 | 1.0 | 0.81, 1.27, 1.57 |
10 | 12 | 1.6 | 0.81, 1.27, 1.57 |
12 | 16 | 1.6 | 0.81, 1.27, 1.57 |
14 | 19 | 1.6 | 0.81, 1.27, 1.57 |
16 | 22 | 1.6 | 0.81, 1.27, 1.57 |
18 | 25 | 1.6 | 0.81, 1.27, 1.57 |
20 | 28 | 1.6 | 0.81, 1.27, 1.57, 2.11 |
22 | 30 | 2.0 | 0.81, 1.27, 1.57, 2.11 |
25 | 34 | 2.0 | 0.81, 1.27, 1.57, 2.11 |
28 | 40 | 2.0 | 0.81, 1.27, 1.57, 2.11 |
30 | 42 | 2.0 | 0.81, 1.27, 1.57, 2.11 |
32 | 45 | 2.0 | 0.81, 1.27, 1.57, 2.11 |
34 | 48 | 2.0 | 0.81, 1.27, 1.57, 2.11 |
36 | 50 | 2.0 | 0.81, 1.27, 1.57, 2.11 |
38 | 52 | 2.0 | 0.81, 1.27, 1.57, 2.11 |
40 | 56 | 2.0 | 0.81, 1.27, 1.57, 2.11 |
42 | 60 | 2.0 | 0.81, 1.27, 1.57, 2.11 |
45 | 63 | 2.0 | 0.81, 1.27, 1.57, 2.11 |
48 | 68 | 2.0 | 0.81, 1.27, 1.57, 2.11 |
50 | 70 | 2.0 | 0.81, 1.27, 1.57, 2.11 |
52 | 75 | 2.0 | 0.81, 1.27, 1.57, 2.11 |
56 | 80 | 2.0 | 0.81, 1.27, 1.57, 2.11 |
60 | 85 | 2.0 | 0.81, 1.27, 1.57, 2.11 |
63 | 90 | 2.0 | 0.81, 1.27, 1.57, 2.11 |
80 | 112 | 3.0 | 1.27, 1.57, 2.11, 3.40 |
100 | 140 | 3.0 | 1.27, 1.57, 2.11, 3.40 |
125 | 180 | 3.0 | 1.27, 1.57, 2.11, 3.40 |
We can quote metric plugs with thicknesses that conform to DIN470 – however if you can work with our stock material the piece price will be more economical, especially for small and medium volume orders.